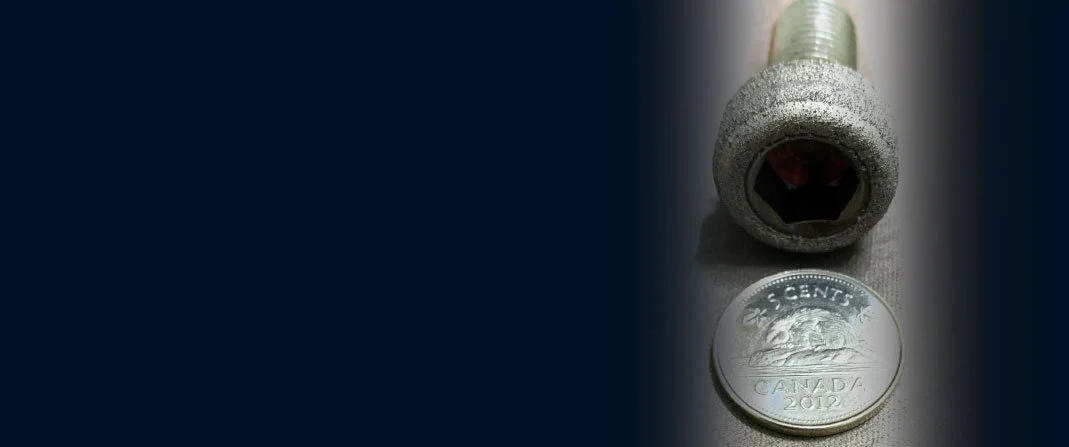
WHEN YOU NEED RELIABLE TIMELINES & DELIVERIES.
As a dedicated shop for laser cladding, we have control over our schedules and can give our customers realistic and reliable turn-around times.
Applications
01 Refurbish Components
When you find your parts have worn beyond what you believe is salvageable, laser cladding is the perfect solution to rebuild your component back to its original size and geometry.
Laser cladding is used to restore components such as shafts, housings, blowers, and spindles to original shape and size. Bearing fits can be brought back to size so that mating parts do not have to be tracked for oversized/undersized configurations, reducing inventory. Seal areas can be built back to nominal size as laser cladding allows thicker layers than chrome.
Let Group Six discuss your specific requirements and determine if there is a more desirable cladding material that is superior to the OEM part.
GET A QUOTE NOW >

WHEREVER HIGH VALUE COMPONENTS ARE USED
02 Seal Surfaces
Laser Cladding can be used to replace chrome in various applications. Group Six has developed a process that allows for a pore free and crack free surface using a 400 series stainless steel alloy.
With laser cladding, a coating can be anywhere from 0.010” to over - 0.250” thick so damaged areas can be repaired without a thickness limitation, unlike chrome.
The hardness of the cladding (50-55HRc) allows the surface to machined, rather than being ground, and can be polished to 4Ra. µin.
GET A QUOTE NOW >
03 Hard Surfacing
No matter what your wear requirements are, Group Six has a solution for almost every scenario, with a variety of material options including Tungsten Carbide with a nickel-based matrix, Iron based alloys, Stellite 1,6, 12 & 21, Colmonoy 69 Alloys.
Group Six has applied laser clad wear coatings on the internals of Centrifuges, internal bearing surfaces and external wear points of drilling tools, ground engaging tools for mining equipment and numerous other components across various industries. Even the head of a stainless steel screw is able to be protected in an erosive environment.
GET A QUOTE NOW >

GET IN TOUCH
04 Various Materials
Group Six laser cladding is the perfect solution to achieve a corrosion resistant surface on a part that is exposed to a compromising environment whether it be air, water, or acids. The advantage of using laser cladding is that the overlay is metallurgically bonded to the base material so, unlike chrome or HVOF, nothing can penetrate through the overlay and corrode the underlying material. For some applications, it makes economic sense to laser clad an inexpensive steel part, with a corrosion resistant alloy. This could be completed at a lower cost than making the entire part out of that same as a corrosion resistant material.